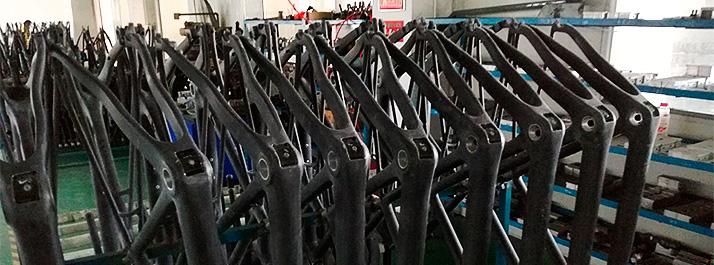
Serce całego roweru. Wykonana z różnego materiału, przeznaczona do różnych zastosowań, ma odpowiadać końcowemu klientowi zarówno pod względem jakości i wyglądu, jak i ceny. Przyjrzyjmy się procesowi produkcji ram rowerowych oraz wyzwaniom, jakie stoją obecnie przed producentami - wszystko na podstawie naszych doświadczeń m.in. przy pracy nad ramą Accent Peak 29.
Każda marka w swojej ofercie posiada różne ramy i budowane na nich rowery. Zanim powstanie finalny projekt, zadaniem producenta jest określenie rodzaju ramy oraz scharakteryzowanie użytkownika, dla którego będzie przeznaczona. To definiuje pewne rozwiązania, które zostaną zastosowane. Najczęściej wykorzystywane materiały to oczywiście aluminium oraz karbon. Zarówno jeden materiał, jak i drugi, ma swoje cechy charakterystyczne, które jednak nie powinny być określane jako wady i zalety, a po prostu właściwości.
Karbon jest obecnie materiałem stosowanym we wszystkich rodzajach ram określanych pojęciem Racing oraz w bardziej zaawansowanych produkcjach. Cechuje go oczywiście niska waga, ale także duża sztywność. Aluminium to nadal materiał najczęściej wybierany do produkcji ram rowerowych. Przy zastosowaniu odpowiedniej obróbki i wykorzystaniu wiedzy o projektowaniu ram możemy osiągnąć bardzo dobre rezultaty zarówno pod względem wagi, jak i sztywności. Przy aluminium nie można pominąć faktu, że gotowy produkt jest dużo tańszy niż bardziej zaawansowany karbon.
Spójrzmy na przykład naszej flagowej ramy Peak 29. Wszystko zaczęło się od wersji wykonanej z aluminium. Określiliśmy grupę odbiorców, rama była dedykowana dla osób z zacięciem sportowym, zaczynających przygodę ze startami na rowerze MTB, jak i jeżdżących, trenujących na góralu. Oczywiście analiza ta była dość dogłębna, ale to są jej główne wnioski. Pozwalają one na zdefiniowanie najlepszej geometrii i parametrów. Wiemy, że rama ta ma stanowić bazę pod rower, który będzie służył do startów w zawodach. Kluczowa więc jest geometria, która sprawia że rower odpowiednio zachowuje się w trudnym terenie. Musimy określić kąty, długości rur, poszczególne parametry takie jak rodzaj sterów, czy środka suportu. Rozpoczyna się praca z inżynierami, którzy z pomocą programów komputerowych pomagają dobrać odpowiednie profile rur, zmniejszyć wagę w mniej obciążonych miejscach poprzez odpowiednie cieniowanie, czy zaplanować wystarczającą ilość miejsca na oponę.
Ramy aluminiowe
W przypadku aluminium można skorzystać z gotowych rurek lub projektować od podstaw własne z uwzględnieniem parametrów, które nas interesują: profilu, cieniowania, kształtu. Każdy element, który tworzymy od zera wymaga otwarcia nowego moldu, którego koszt musi być później uwzględniony w końcowej wycenie projektu. Co ciekawe, koszty mogą sięgać nawet kilkudziesięciu tysięcy dolarów.
Na podstawie wszystkich wytycznych inżynierów powstaje rysunek lub model 3D. Po jego zaakceptowaniu tworzony jest prototyp ramy. W wielu przypadkach takie elementy jak tylne haki lub elementy zawieszenia tworzone są pierwotnie za pomocą obróbki CNC. Taki element jest droższy niż w finalnej wersji, ale pozwala na ewentualne korekty i zmiany. Wybiera się również rodzaj stosowanych spawów, które mają wpływ na parametry oraz na wygląd ramy.
Często prototyp udaje się wstępnie pomalować i okleić naklejkami, żeby jak najwierniej przypominał wersję finalną projektu. Samo wykończenie graficzne daje bardzo duże pole manewru. Warto wspomnieć, że na Tajwanie są firmy specjalizujące się wyłącznie w naklejkach na ramy i rowery. Do wyboru mamy: płaskie, wypukłe, zmieniające kolor... Każda marka ma swój kierunek graficzny, w którym podąża i który charakteryzuje ją na tle innych.
Przeważnie powstaje kilka prototypów, które trafiają na testy do zawodników – ci sprawdzają właściwości jezdne, inne są testowane na maszynach, by potwierdzić, że spełniają wymogi stawiane ramom przez normy. Jeżeli wszystkie parametry w prototypach zostaną zaopiniowane pozytywnie, wszystko do siebie pasuje, naniesione są poprawki – można otwierać odpowiednie moldy. Po sprawdzeniu kolejnych szczegółów, takich jak ułożenie przelotek, mocowania koszyka na bidon, mocowania kabli, rama trafia do produkcji.
Sama produkcja ram rozpoczyna się od zebrania wszystkich przygotowanych rurek i elementów w jednym miejscu. Kolejne podzespoły są spawane w założonej kolejności. Ważne jest, żeby wszystkie elementy były osiowe, by gwinty były w odpowiednich płaszczyznach oraz by zachowane były tolerancje otworów. Do tego niezbędne są stoły spawalnicze, frezy, gwintowniki. Na każdym etapie niezbędne jest zachowanie odpowiednich procedur, aby gotowa rama spełniała wszystkie założone kryteria.
Wśród Waszych pytań pojawiło się to o cieniowanie rur aluminiowych. To proces, który pozwala na "odchudzenie" ram w celu zbicia ich wagi, ale jedynie w miejscach, gdzie nie wpłynie to na ich wytrzymałość. W przypadku podwójnego cieniowania, najczęściej stosowanego, na końcach rury przy łączeniu z kolejną ścianki są grubsze, a w środku cieńsze.
Ramy karbonowe
W przypadku ram karbonowych, materiałem dostarczanym do fabryki są role z nawiniętymi włóknami. Materiał ten może mieć różne parametry w zależności do czego dokładnie ma być wykorzystywany. Tak dostarczone włókno powinno być przechowywane w odpowiedniej temperaturze i wilgotności, gdyż ma to wpływ na późniejszą jakość samego produktu. Z rolki włókno jest rozwijane, a następnie cięte na paski, trójkąty i inne kształty, zależnie od elementu, do którego stworzenia ma być użyte.
Takie włókno nawijane jest na odpowiednie formy i wstępnie kształtowane. Wszystko odbywa się w ściśle ustalonej kolejności. Ważny jest zarówno kształt, jak i kierunek ułożenia.
Formy są zamykane i tak przygotowane elementy trafiają do pieca w celu ich utwardzenia. Poszczególne elementy, podobniej jak w przypadku produkcji ram aluminiowych, muszą być ze sobą połączone. Może się to odbyć w różny sposób, najbardziej popularną metodą jest wykonywanie większych kawałków, zamiast łączenia małych pojedynczych. Często stosuje się połączenie w jeden element górnej rury i dolnej rury z mufą sterową. Dzięki temu możemy zredukować wagę oraz wraz z odpowiednim ułożeniem włókien – zwiększyć sztywność
Stosowany profil ułożenia włókien i ich rodzaj to strzeżona tajemnica producentów. Co jakiś czas słyszymy, że dany model ramy jest lżejszy, sztywniejszy od poprzednika o ileś procent – to właśnie dzięki stosowaniu nowego sposobu ułożenia kawałków włókna węglowego. Możemy zastosować ich mniej dla redukcji wagi, a odpowiednie ich ułożenie powoduje, że rama jest sztywniejsza. Wszystko to kwestia znalezienia „złotego środka”.
Podobnie jak w przypadku aluminium, poszczególne elementy karbonu łączy się w całość na stole. Ogromnie ważna jest centryczność i ułożenie kolejnych części względem siebie. Szczególnej precyzji wymagają ramy zawieszone, gdzie występują elementy ruchome. Niezbędnym jest, aby łożyska były w odpowiedniej płaszczyźnie i by wszystko razem czysto pracowało. Przygotowana całość jest polerowana i szlifowana.
Różne fabryki posiadają różny stopień kontroli jakości. Można powiedzieć, że poszczególne ramy tym właśnie różnią się między sobą. Popularne „chińczyki” często wydają się takie same jak produkty markowe, ale nie są w taki sam sposób kontrolowane w czasie procesu produkcji. W przypadku naszych ram Accent, podczas każdego etapu produkcji na miejscu znajduje się osoba odpowiedzialna za kontrolę jakości: począwszy od dostarczenia materiału, jego sposobu przechowania, poprzez każdy kolejny powstający element aż to gotowej ramy. Sprawdzamy czy wszystkie części są centryczne, czy zachowane są tolerancje otworów, czy wszystkie połączenia są wykonane zgodnie z założeniami, czy nie ma żadnych wad lakierniczych i powłoka jest jednolita. To daje pewność, że rama, która trafi do klienta spełni jego oczekiwania
Dlaczego Tajwan i Chiny?
Obecnie większość ram rowerowych produkowana jest na Tajwanie i w Chinach. Powodów jest kilka. To właśnie na Dalekim Wschodzie znajduje się zagłębie fabryk pracujących zarówno na aluminium, jak i na karbonie. Są one mocno wyspecjalizowane w tym kierunku, posiadają odpowiedni sprzęt i know-how. Co więcej, w tym samym miejscu znajdują się firmy specjalizujące się w produkcji odpowiednich podzespołów takich jak rury do ram, różne wersje przelotek, haki itd. Plusem jest produkowanie wszystkich części składowych w jednej lokalizacji, co umożliwia sprawny montaż, w którego skład wchodzi także malowanie czy oklejanie ram. Pozwala to na produkcje na skalę masową oraz przygotowanie finalnego produktu, który zadowoli końcowego klienta pod względem jakości, ale także ceny, która spotka się z jego oczekiwaniami.
Co jakiś czas słyszymy o przenoszeniu produkcji do Europy. Dzieje się tak dlatego, że rynek tajwański, a przede wszystkim chiński zmienia się. Coraz więcej wagi przywiązuje się do ochrony środowiska i godziwego traktowania pracowników. Za tym idzie wzrost kosztów. Do tego dochodzi transport, który jest kosztowny i czasochłonny. Obecnie stosunkowo łatwiej jest otworzyć fabrykę pozwalającą na produkcję ram karbonowych, niż aluminiowych. Włókno węglowe dostarczane jest w rolach i z niego możemy uformować praktycznie dowolny kształt, pozwala to zróżnicować produkcję. Z pewnością firmy coraz więcej inwestują w rozwój i szukają nowych możliwości produkcyjnych .
Wyzwania producentów
Proces tworzenia ram jest pracochłonny i kapitałochłonny. Wymaga wielu testów i złożonych operacji. Całość przygotowania projektu zajmuje od kilku miesięcy do roku lub dłużej. Niezależnie od tego czy pracujemy na aluminium czy na karbonie, ważne jest aby dokładnie znać i rozumieć procesy produkcyjne, umieć wykorzystać obecne technologie w zakresie optymalizacji parametrów technicznych, jak i samych procesów. To wszystko wpływa na finalną cenę produktu. Drugim istotnym wyzwaniem jest wspomniana wyżej kontrola jakości. Dzięki temu jesteśmy w stanie dostarczyć produkt atrakcyjny pod względem cenowym, ale też spełniający pozacenowe oczekiwania klientów.
W przypadku naszej aluminiowej ramy Peak 29, po jej sukcesie na rynku, ale także po zebraniu uwag od zawodników i testerów, zaczęliśmy pracę nad karbonowym odpowiednikiem. Wykorzystaliśmy to, co najlepsze w Peaku dodając nowe rozwiązania i technologie. To również proces czasochłonny, wymagający wielokrotnych wizyt w fabryce w celu szukania najlepszych rozwiązań. Warto wspomnieć, że sam okres testowania przez zawodników zajął ponad rok.
Tekst i zdjęcia: Paweł Wiendlocha – brand manager marki Accent. Przez wiele lat ścigał się w maratonach MTB i przełajach, obecnie wykorzystuje wiedzę i doświadczenie tworząc markę rowerów, części i akcesoriów. Odpowiada za cały proces powstawania produktu.